立式磨粉機(jī)主要由選粉機(jī)、磨輥裝置、磨盤(pán)裝置、加壓裝置、減速機(jī)、電動(dòng)機(jī)、殼體等部分組成。分離器是一種高效、節(jié)能的選粉裝置。磨輥是用來(lái)對(duì)物料進(jìn)行碾壓粉碎的部件。磨盤(pán)固定在減速機(jī)的輸出軸上,是磨輥碾壓物料的地方。加壓裝置是為磨輥提供碾壓力的部件,向磨輥提供足夠的壓力以粉碎物料。
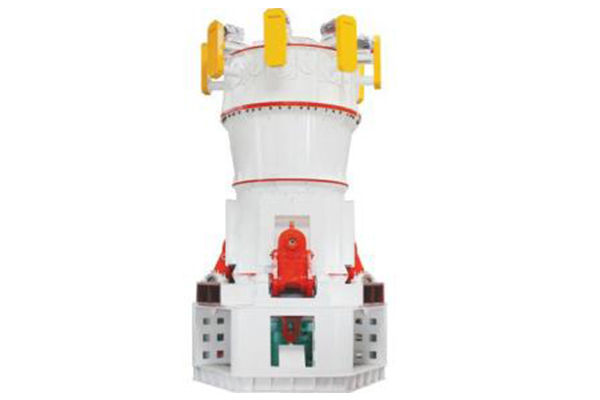
立磨磨輥本體和耐磨襯板在使用過(guò)程中,由于受到輥?zhàn)幽雺毫?、物料支反力、物料與磨輥襯板之間的摩擦阻力;由于物料碾入角而造成磨輥剪切應(yīng)力、輥磨的液壓系統(tǒng)壓力以及立磨的表觀壓應(yīng)力等力的相互綜合作用,這些力均作用于立磨磨輥有效碾壓區(qū)。
一旦出現(xiàn)配合間隙,本體與襯板之間將會(huì)發(fā)生沖擊碰撞,使得本體與襯板之間磨損加劇,嚴(yán)重時(shí)使得襯板產(chǎn)生裂紋甚至斷裂,造成襯板脫落,機(jī)器損壞,特別是減速機(jī)的損壞,造成惡性事件。該類問(wèn)題一旦發(fā)生,一般修復(fù)方法難以解決,拆卸、焊補(bǔ)、機(jī)加工費(fèi)時(shí)費(fèi)力,造成的停機(jī)停產(chǎn)時(shí)間大大延長(zhǎng),給企業(yè)帶來(lái)無(wú)可挽回的巨額經(jīng)濟(jì)損失。針對(duì)上述問(wèn)題,歐美等發(fā)達(dá)多使用高分子復(fù)合材料進(jìn)行立磨輥體磨損快速修復(fù),材料以其優(yōu)良的機(jī)械性能及良好的可塑性,使得該問(wèn)題得以圓滿解決。
不僅可延長(zhǎng)設(shè)備使用壽命、提高生產(chǎn)率,并且在不占用額外的停機(jī)停產(chǎn)時(shí)間的同時(shí),簡(jiǎn)單有效的避免該問(wèn)題出現(xiàn)的二次可能性,給企業(yè)安全連續(xù)化生產(chǎn)保駕護(hù)航。立磨磨輥軸承的裝配要求比較嚴(yán)格,企業(yè)一般采用將軸承放在干冰中冷卻的方式裝配。軸承和軸承室之間一旦出現(xiàn)間隙,將會(huì)影響軸承的正常運(yùn)轉(zhuǎn),導(dǎo)致軸承發(fā)熱,嚴(yán)重時(shí)將會(huì)導(dǎo)致軸承燒結(jié)現(xiàn)象。傳統(tǒng)補(bǔ)焊刷鍍等方法存在一定的弊端:補(bǔ)焊會(huì)產(chǎn)生熱應(yīng)力造成軸承材質(zhì)受損,嚴(yán)重時(shí)會(huì)變形甚至斷裂;刷鍍污染較重,且鍍層厚度受限,應(yīng)用受到較大限制。
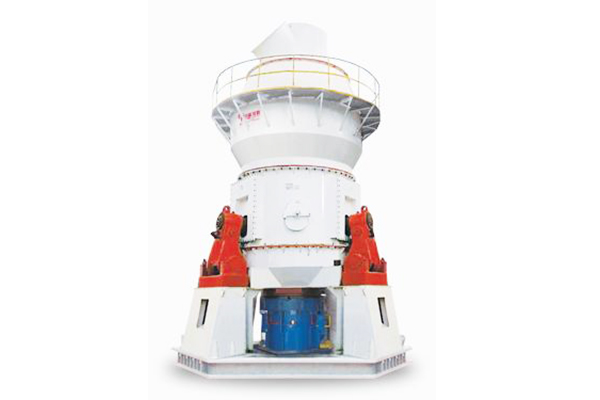
高分子復(fù)合材料既具有金屬所要求的強(qiáng)度和硬度,又具有金屬所不具備的退讓性(變量關(guān)系),通過(guò)“模具修復(fù)”、“部件對(duì)應(yīng)關(guān)系”、“機(jī)械加工”等工藝,可以大限度確保修復(fù)部位和配合部件的尺寸配合;同時(shí),利用復(fù)合材料本身所具有的抗壓、抗彎曲、延展率等綜合優(yōu)勢(shì),可以有效地吸收外力的沖擊,極大化解和抵消軸承對(duì)軸的徑向沖擊力,并避免了間隙出現(xiàn)的可能性,也就避免了設(shè)備因間隙增大而造成的二次磨損。
立式磨粉機(jī)正常工作時(shí),電動(dòng)機(jī)通過(guò)減速機(jī)帶動(dòng)磨盤(pán)轉(zhuǎn)動(dòng),物料經(jīng)鎖風(fēng)喂料器從進(jìn)料口落在磨盤(pán)中央,同時(shí)熱風(fēng)從進(jìn)風(fēng)口進(jìn)入磨內(nèi)。隨著磨盤(pán)的轉(zhuǎn)動(dòng),物料在離心力的作用下,向磨盤(pán)邊緣移動(dòng),經(jīng)過(guò)磨盤(pán)上的環(huán)形槽時(shí)受到磨輥的碾壓而粉碎,粉碎后的物料在磨盤(pán)邊緣被風(fēng)環(huán)高速氣流帶起,大顆粒直接落到磨盤(pán)上重新粉磨,氣流中的物料經(jīng)過(guò)上部分離器時(shí),在旋轉(zhuǎn)轉(zhuǎn)子的作用下,粗粉從錐斗落到磨盤(pán)重新粉磨,合格細(xì)粉隨氣流一起出磨,通過(guò)收塵裝置收集,即為產(chǎn)品,含有水分的物料在與熱氣流的接觸過(guò)程中被烘干,通過(guò)調(diào)節(jié)熱風(fēng)溫度,能滿足不同濕度物料要求,達(dá)到所要求的產(chǎn)品水分。通過(guò)調(diào)整分離器,可達(dá)到不同產(chǎn)品所需的粗細(xì)度。